XJTU-SY滚动轴承加速寿命实验数据集 / XJTU-SY Bearing Datasets
Dataset Overview
XJTU-SY bearing datasets are provided by the Institute of Design Science and Basic Component at Xi’an Jiaotong University (XJTU), Shaanxi, P.R. China and the Changxing Sumyoung Technology Co., Ltd. (SY), Zhejiang, P.R. China. The datasets contain complete run-to-failure data of 15 rolling element bearings that were acquired by conducting many accelerated degradation experiments. These datasets are publicly available and anyone can use them to validate prognostics algorithms of rolling element bearings. Publications making use of the XJTU-SY bearing datasets are requested to cite the following paper.
- Biao Wang, Yaguo Lei, Naipeng Li, Ningbo Li, “A Hybrid Prognostics Approach for Estimating Remaining Useful Life of Rolling Element Bearings”, IEEE Transactions on Reliability, vol. 69, no. 1, pp. 401-412, 2020.
Bearing Testbed & Tested Bearing
As shown in the following figure, the bearing testbed is composed of an alternating current (AC) induction motor, a motor speed controller, a support shaft, two support bearings (heavy duty roller bearings), a hydraulic loading system and so on. This testbed is designed to conduct the accelerated degradation tests of rolling element bearings under different operating conditions (i.e., different radial force and rotating speed). The radial force is generated by the hydraulic loading system and applied to the housing of tested bearings, and the rotating speed is set and kept by the speed controller of the AC induction motor.
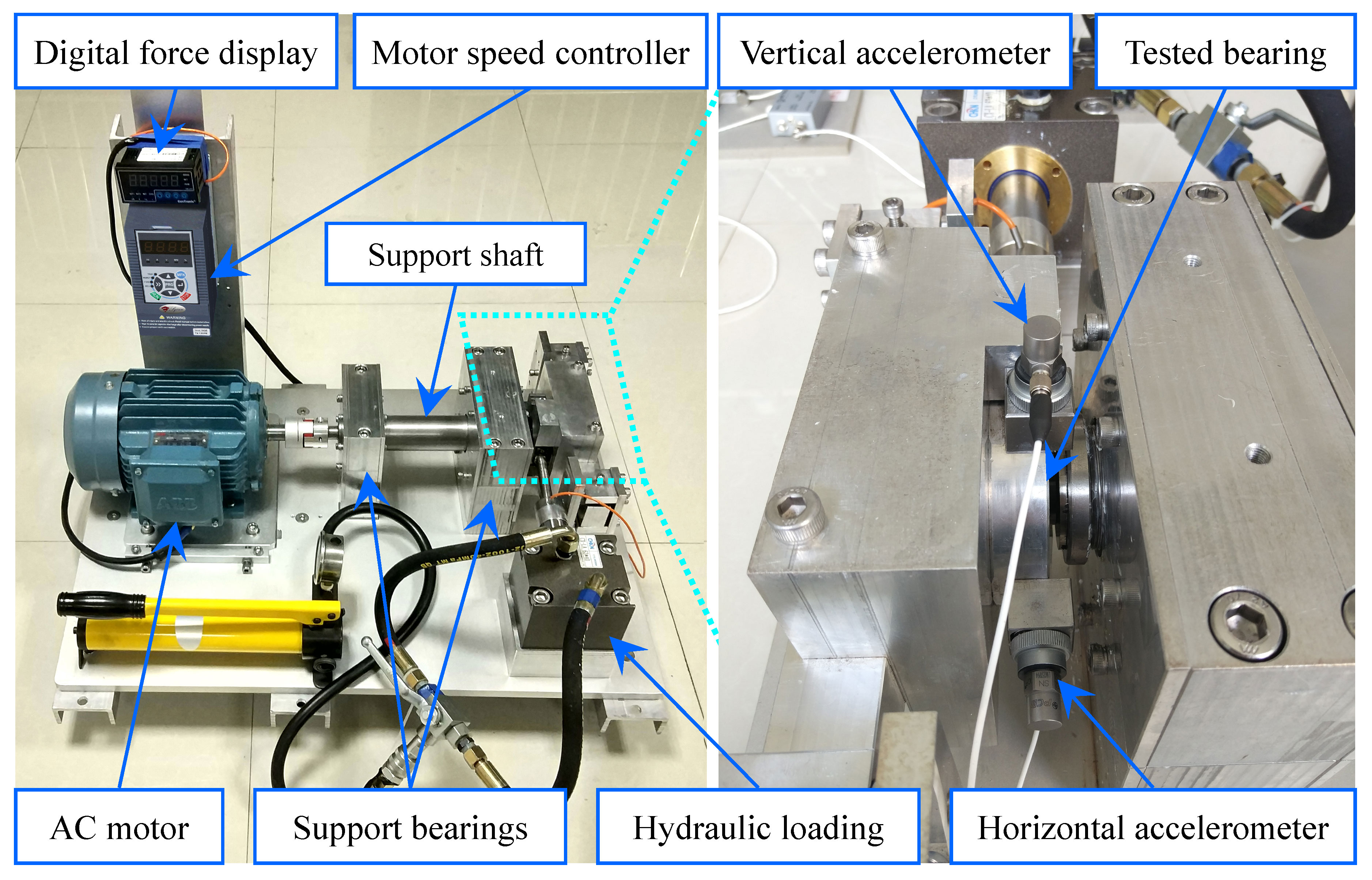
The type of tested bearings is LDK UER204, and the detailed parameters are given in the following table.
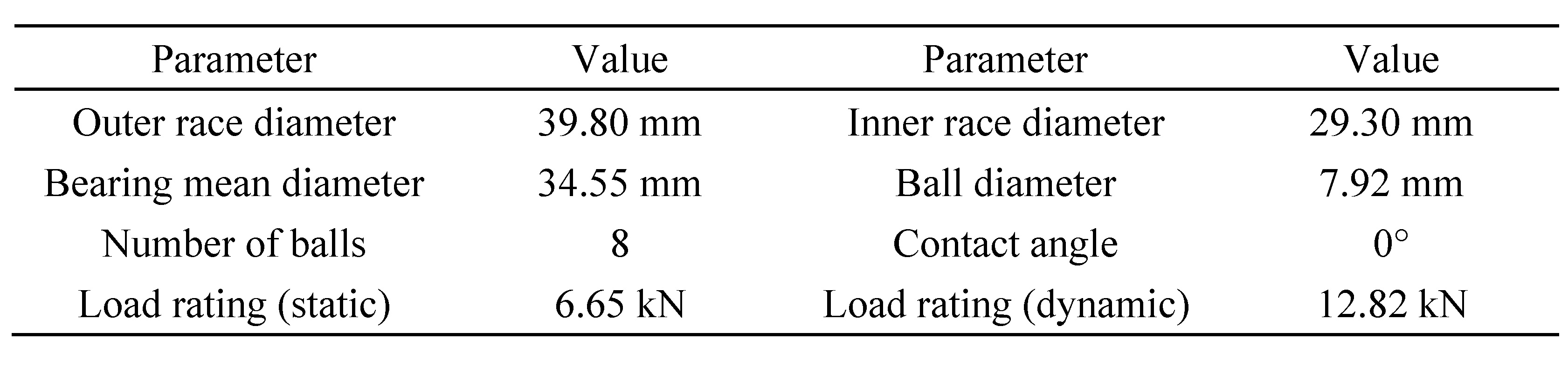
Operating Condition & Sampling Setting
A total of 3 different operating conditions were set in the accelerated degradation experiments, and 5 bearings were tested under each operating condition. The operating conditions include: ① 2100 rpm (35 Hz) and 12 kN; ② 2250 rpm (37.5 Hz) and 11 kN; ③ 2400 rpm (40 Hz) and 10 kN.
To collect vibration signals of the tested bearings, two accelerometers of type PCB 352C33 are positioned at 90° on the housing of the tested bearings, i.e., one is mounted on the horizontal axis and the other one is mounted on the vertical axis. The sampling frequency is set to 25.6 kHz. A total of 32768 data points (i.e. 1.28 s) are recorded for each sampling, and the sampling period is equal to 1 min.
Dataset details
The run-to-failure data of 15 rolling element bearings are included in the data packet (XJTU-SY_Bearing_Datasets.zip). For each sampling, the acquired data were saved as a CSV file, in which the first column is the horizontal vibration signals and the second column is the vertical vibration signals. The following table lists the detailed information of each tested bearing, including number of CSV files, bearing lifetime and fault element.
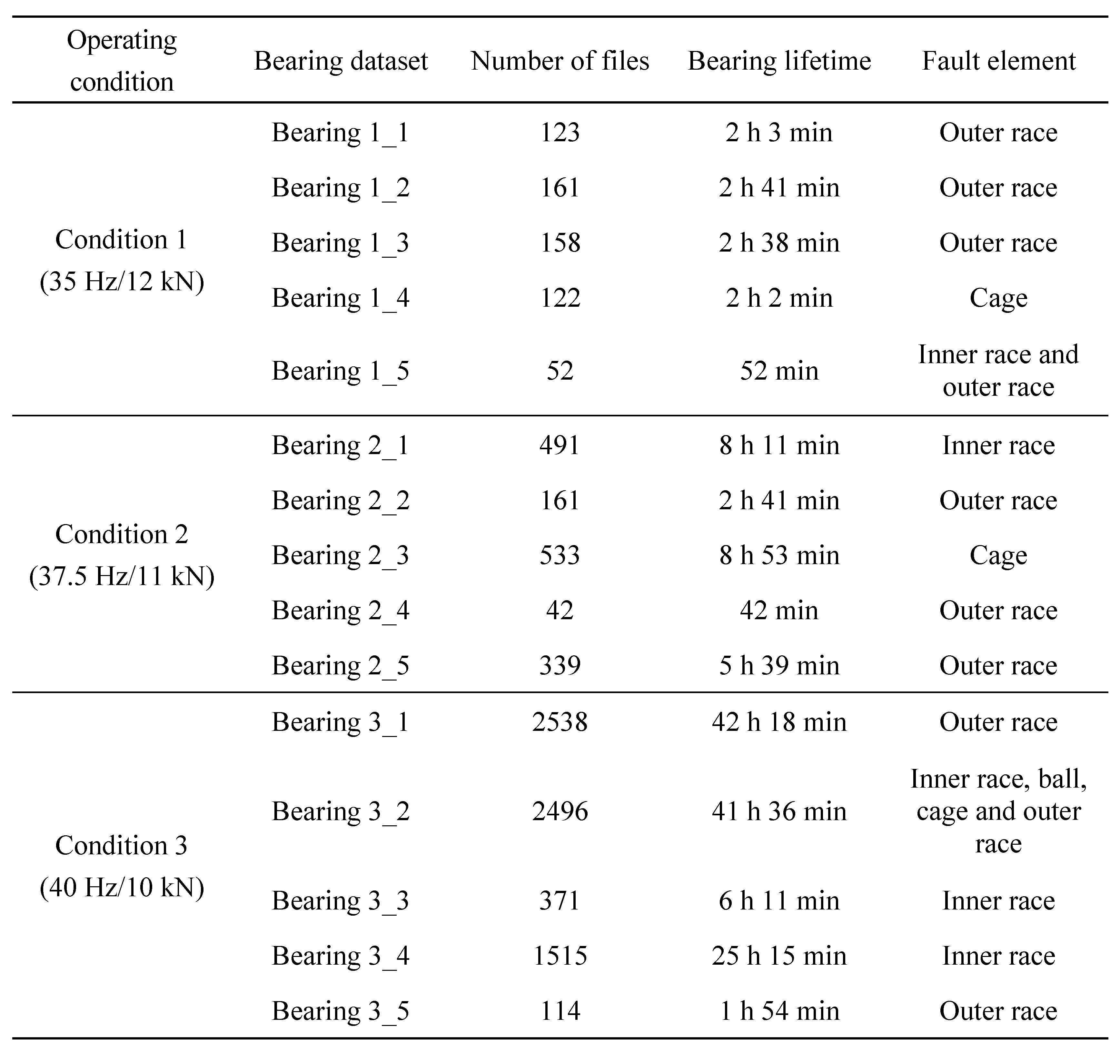
The following figure shows the photographs of the failure bearings. It can be observed that the failure of the tested bearings is caused by different types of faults, including inner race wear, cage fracture, outer race wear, outer race fracture, etc.
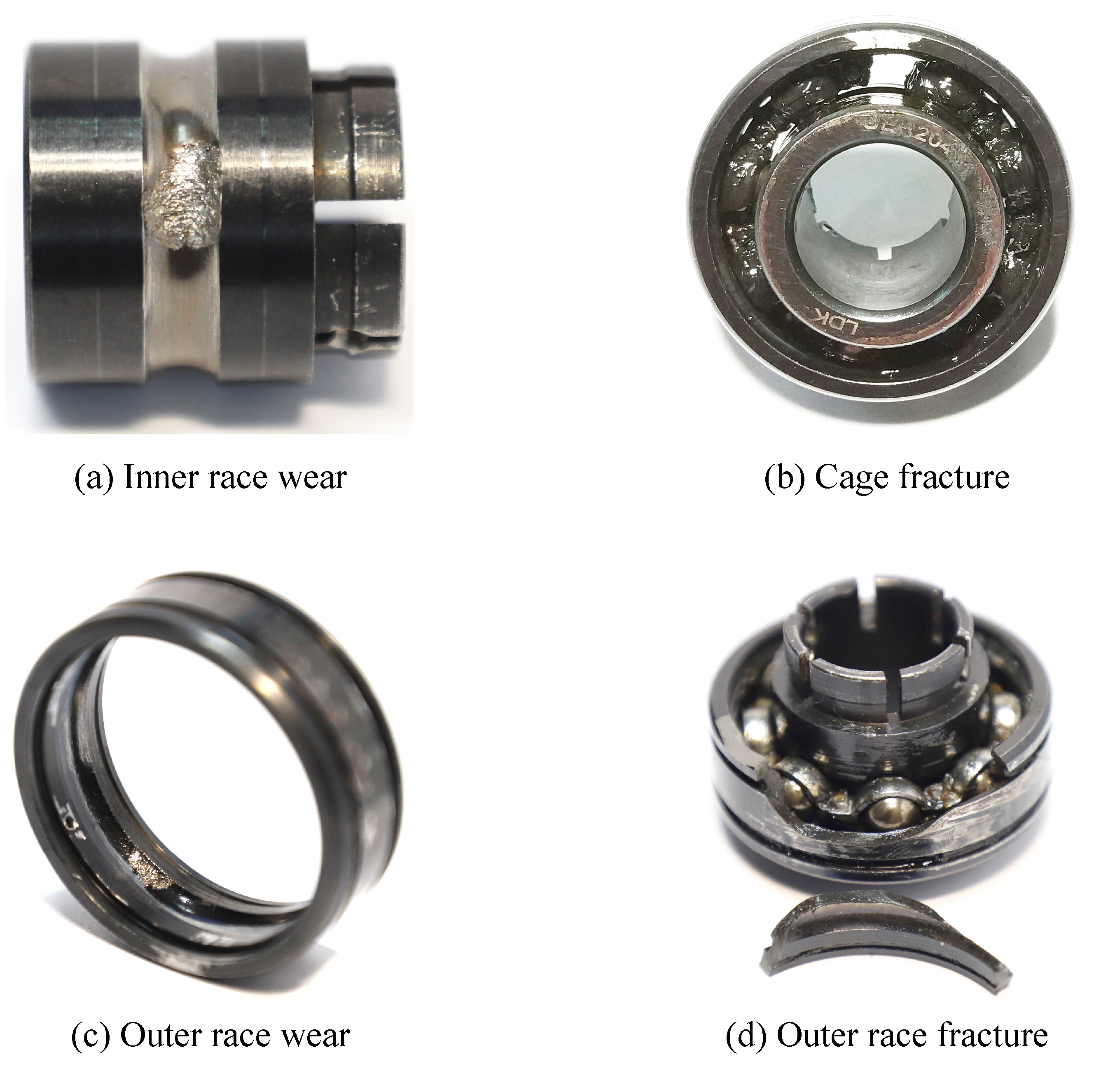
The following figure shows the horizontal and vertical vibration signals of three tested bearings during the whole operating life.
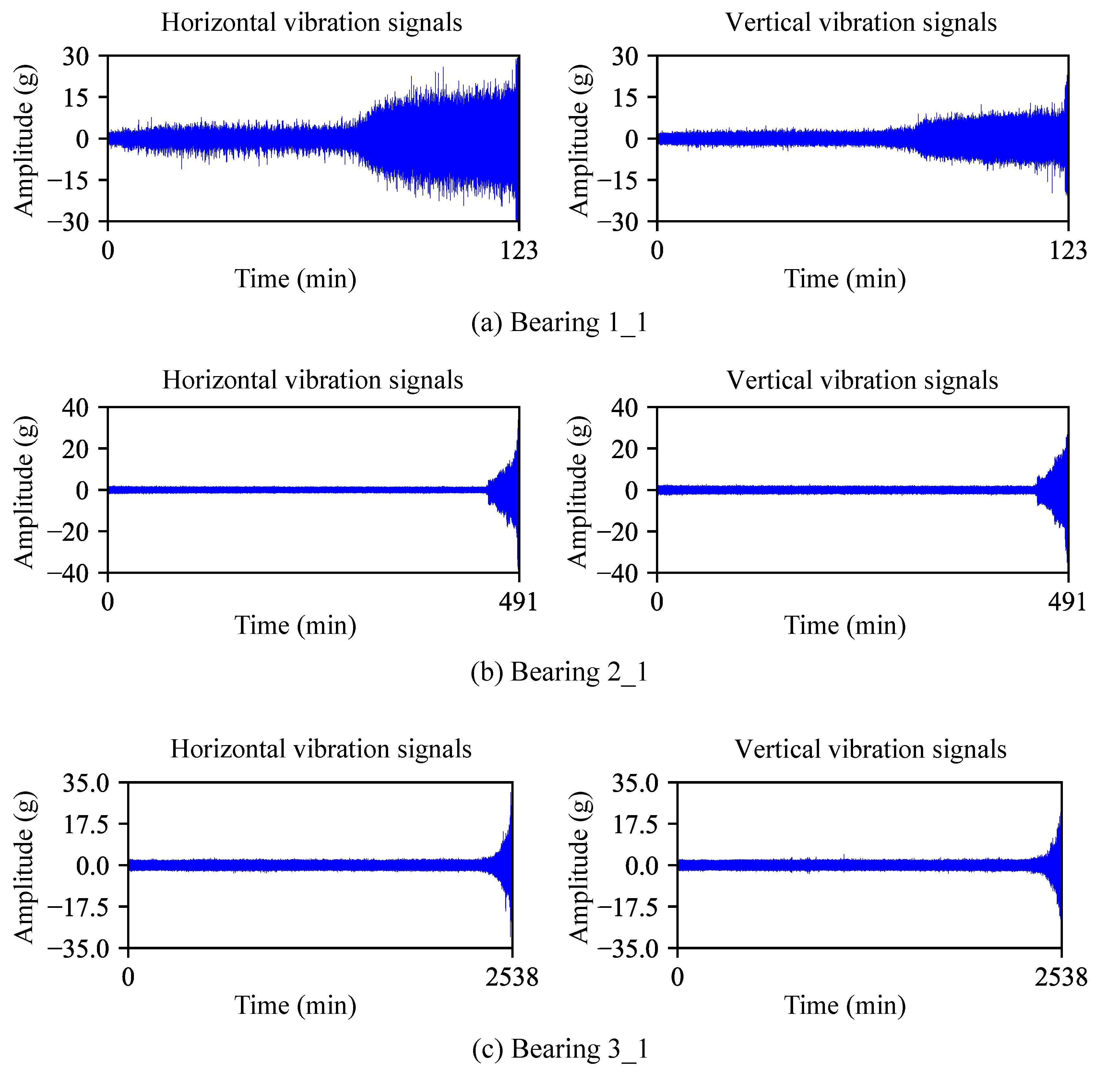
Download links
XJTU-SY bearing datasets can be downloaded by one of the following links:
- My Website: http://biaowang.tech/xjtu-sy-bearing-datasets
- Google Drive: https://drive.google.com/open?id=1_ycmG46PARiykt82ShfnFfyQsaXv3_VK
- Dropbox: https://www.dropbox.com/sh/qka3b73wuvn5l7a/AADr6oXKbafhOlrBLCNgonzua?dl=0
- MediaFire: http://www.mediafire.com/folder/m3sij67rizpb4/XJTU-SY_Bearing_Datasets
- MEGA: https://mega.nz/#F!H7pnGKBK!PR8qUShaLlJjwrPf3SlBjw
- Baidu Netdisk: https://pan.baidu.com/s/1OaY82azTXHBwjiCjA_jRcw